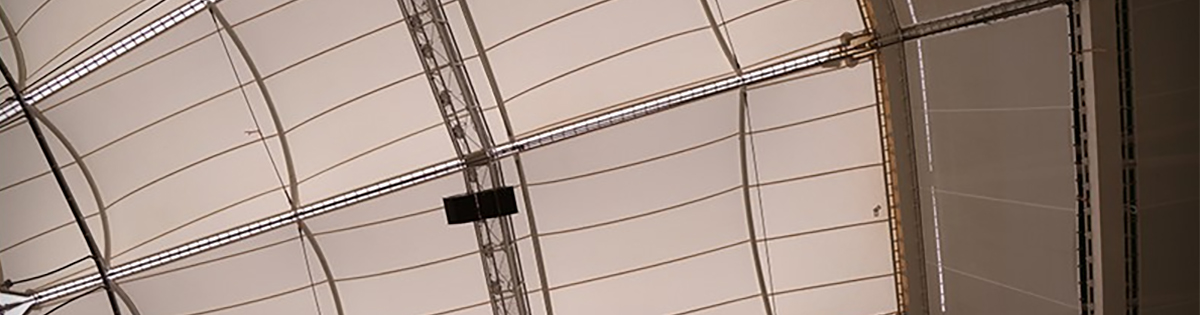
The manufacturing process starts after the membrane details, welding and membrane plate types are determined according to the project specifications and static calculations.
![]() | SURFACE CONTROL: The membrane rolls received from the manufacturer go through surface controls against deformations and flaws that may occur on their surfaces during the manufacturing phase. |
![]() | STATICAL STRENGTH TEST: Resistance and welding strength tests are carried out by independent laboratories to determine whether the material produced have the strengths stipulated, and to obtain static values to constitute basis for our engineering calculations. After passing these tests, the rolls are packed and dispatched to our manufacturing facilities. |
![]() | CUTTING: The materials received as rolls are cut with +/-1mm accuracy in CNC-controlled automatic machines in compliance with the cutting panels formed. The templates cut are turned into rolls and taken to the welding line. |
![]() | FEP FILM WELDING: The PTFE membrane templates cut are fixed to one another at points via FEP films. |
![]() | IRONING: The template lines with FEP films placed in-between are fixed to one another via ironing, and made ready for welding by hot bar press machines. |
![]() | MEASURE CONTROL: The template lines with FEP films placed in-between are fixed to one another via ironing, and made ready for welding by hot bar press machines. |
![]() | HOT BAR PRESS WELDING: Conformity of the welded templates to the project measurements are checked before the hot bar press welding. |
![]() | PACKAGING: The materials controlled in terms of measures are made ready for the packaging process after being welded with a hot bar press machine. |
![]() | TRANSPORTATION: The packaged PTFE membrane materials are sent to the construction site for installation. |